Als service organisatie voor gasturbine motoren moet je 24/7 klaarstaan. De betrouwbaarheid van jouw product bepaald in grote mate de energiekosten in o.a. de tuinbouwsector. MWM Benelux heeft een uitstekende reputatie op dit gebied waarbij naast reparaties ook preventief onderhoud en het compleet overhalen in het pakket wordt meegenomen. Vak gedreven medewerkers die op elk moment van de dag elke technische klus kunnen klaren. Toch komt er meer bij kijken dan alleen techniek.
MWM Benelux – Brengt flow in onderhoud
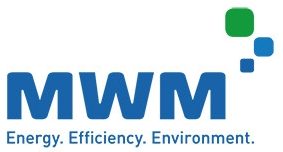
Nog steeds denken velen dat Lean alleen maar iets is voor grote assemblage bedrijven. Veel “seriematig werk” maakt Lean werken mogelijk. En zeg nou zelf: reparaties zijn onvoorspelbaar dus vraagt om echte “brandweer” mensen die dag en nacht klaar staan. Echter het tegenovergestelde is waar! Gelukkig dacht het management van MWM Benelux er ook zo over waarna LMP werd gevraagd om ook dit proces Lean te maken. Met de ruime ervaring op het gebied van project organisaties en repair & maintenance bedrijven kon LMP vlot aan de slag waarbij als eerste werd gekeken hoe de actuele flow nu eigenlijk verliep. Door samen met de betreffende medewerkers dit proces te doorlopen kwamen al snel tal van kleine maar ook grote zaken aan het licht. Kleine aanpassingen in werkvolgorde van de organisatie die zonder kosten snel konden worden doorgevoerd gaven vaak al verrassende resultaten. Kaizen events boden hier uitkomst. De grotere verbeterprojecten werden op prioriteit ingedeeld waarbij de haalbaarheid en de risico’s inzichtelijk werden via de z.g.n. critical-to matrix. Dankzij het enthousiaste team van medewerkers die met heldere doelstellingen aan de slag gingen kwamen er ook al snel veel spontane verbeteractiviteiten bij.
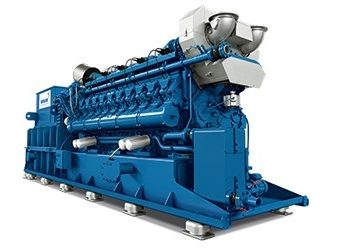
Ook bij dit bedrijf bleek het opsplitsen van specifieke flows van belang om de voorspelbaarheid van het proces beter te kunnen managen waarna de 7 pilaren uit het TPM programma van Lean op elke van die flows konden worden toegepast. Alle onderdelen van het proces zoals de order intake (CLean), werkvoorbereiding, magazijn, logistiek (inkoop/magazijn) en reparatie zijn daarbij onder de loop genomen. Na de organisatorische kant kwam ook al snel de behoefte om specifieke onderhouds intervallen nader te onderzoeken. Met behulp van Six Sigma technieken werd de betrouwbaarheid rondom de levensduur van kostbare onderdelen in kaart gebracht. Door te segmenteren in omgevingscondities en gebruiksbelasting kon hier al snel geld en tijd worden bespaard.
Het door LMP verzorgde Lean traject gaf MWM een goede boost om scherper in te gaan zetten op de aanpak verspillingen die zowel op technisch maar ook op organisatorisch vlak aanwezig waren. Met een gedreven team en een heldere doelstelling werden tal van verspillingen intern in no-time weggewerkt. Een fantastische prestatie!