Yes, this is usually possible. Many companies allow a 50% reduction in both lead time and inventory due to process improvement. Maintaining or even improving delivery reliability at the same time is paramount.
Programs such as Lean Manufacturing and World Class Manufacturing provide good guidance for achieving the stated objectives. To achieve a balanced objective, a Lean quick scan can be performed. For this, use is made of a so-called Value Stream Map (VSM), which is elaborated for the current and the new desired situation. This already gives a good idea of the improvement potential with regard to lead time, stock level and failure costs.
FAQ
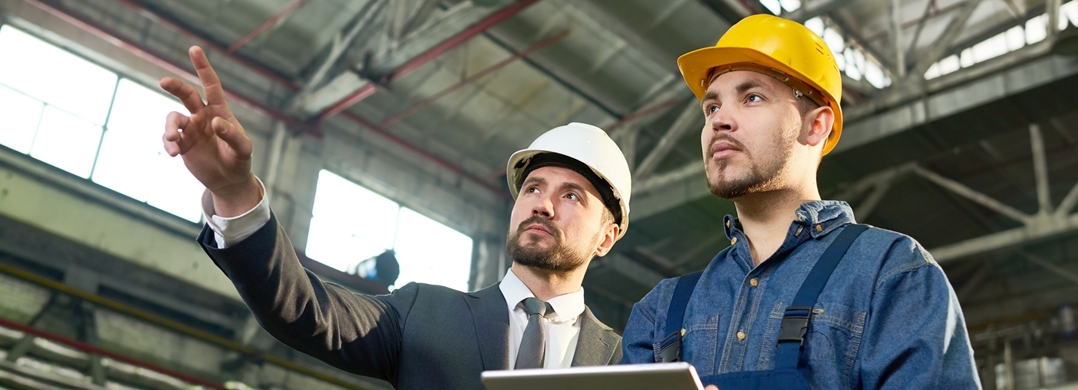
Lean is a philosophy that forms the basis of a business model. However, many common optimization programs are based on existing structures.
In that sense, Lean can be seen as a collection of practical tools that make it possible to apply the Lean philosophy within a company. Where companies usually assume a functional structure with specialist departments, the Lean philosophy is based on Flow per product family group. Within these groups, all people involved are linked to a specific flow, which means that there is more focus for the customer’s interests. Flow is usually less easy to realize within a functionally organized organization. This makes Lean unique from most other improvement programs.
Lean is definitely part of a company’s strategy. If Lean is used to help support a company’s mission and vision, this means that a multi-year plan is drawn up in which the Lean philosophy is rolled out in steps using the appropriate “tools”.
Lean never ends. In the “maturity” models from the Lean program a clear picture is drawn on how this evaluation must take place. Where companies are initially strongly focused on the implementation of the basic tools such as 5-S, companies will soon make a deepening step by also implementing organizational changes. For example, a major pioneer of Lean in the Netherlands is Scania. Their Lean program is “only” 20 years old, whereby people themselves indicate that they see sufficient points for improvement for the near future with which the Lean philosophy has not yet been elaborated. In addition, it is striking that the need and initiation of a Lean program per company can come from different disciplines. HRM, finance and sales departments often lead the way for a variety of reasons.
The answer to this question is simply nothing! In fact, it should generate money from day one!
Of course the answer is a bit more nuanced, but implementing the Lean philosophy means working smarter. By working smarter you free up time that you can invest in the next improvement or, if necessary, in increasing the output. Now you can hear companies sometimes saying that by purchasing a new welding robot or spray booth, they have been able to significantly increase their capacity and have thus become Lean. Unfortunately, this is incorrect. Apart from whether or not such an investment makes sense (Lean makes no statement about that), Lean is primarily focused on Flow and thus eliminating waste. To increase the chances of success with the introduction of Lean and to avoid the usual pitfalls, it is advisable to attract an experienced Lean person. For larger organizations this can be an own employee and for SMEs, for example, a recognized organization with a good track record. In all cases, the pay-back time must be demonstrable in the short term!
Lean is a philosophy and a strategy to eliminate all forms of waste in an organization. Lean is supported by a set of operational, very practical tools.
Lean is applicable to all possible business processes (after all, where is there no waste whatsoever?), Such as in production, order entry, product design and customer service. The Lean steps are divided into 5 groups, with specific activities defined in each group. Flow, Pull and Waste are the core of the program. Given the size and impact of a full Lean program, organizations usually take 3 to 4 years for a complete turnaround, until continuous improvement is in the DNA of the organization. However, the first visible results can often be measured within a year, if a well thought-out approach is chosen. The program has a strong top-down approach based on the mission vision & strategy and subsequent KPIs. However, the Bottum-up is also clearly recognizable, whereby responsibilities are placed low in the organization and an appeal is made to the knowledge and creativity of everyone. The often heard slogan “Lean & Mean” can wrongly evoke a negative association with organizational downsizing or disguised cost-cutting. As a rule, growth through strengthening the competitive position is the starting point when introducing Lean: doing more with the same resources. This is partly made possible by the more efficient working method and shorter turnaround times.
Although Lean was created and further developed in the typical assembly companies such as the automotive industry, the developments surrounding process optimization tools have continued as a result of which service & service companies have also started to use Lean on a large scale as a tool to achieve their goals.
There are even many successful examples of Lean applications in municipalities, hospitals, banks and insurance companies today. Lean’s 5 basic steps have always remained the same for all types of organizations. However, not all Lean tools can always be used everywhere. The use of the tools differs per organization and depends strongly on the desired objectives. In addition, the possible impact of a Lean program can also vary greatly per organization. Apart from the effort level, a sole proprietorship will benefit relatively less from a Lean program than a multinational.
The basic principles of Lean are about optimizing processes by eliminating waste. This means that Lean can often also produce remarkable results in an office environment on the aspects of speed (lead time), quality of output and required resources (including man-hours).
The reliability of the processes is of primary importance. Lean is therefore perfectly applicable in almost any office environment. Important elements are: determining the current and future desired situation through the Business Value Stream map, determining the activities via the Roadmap and then structurally optimizing through a Continuous Improvement Cycle. LMP actively supports Lean office projects within various organizations where the Finance, Sales, Purchasing, Planning, IT, HR and of course management departments are the primary focus area.
When utilizing all the resources within the company to the maximum, the costs are rising faster than what can be expected on the basis of the actual order book. By starting immediately with the elimination of the primary wastes by means of the Pareto analysis, the resources are less burdened and there is again a balance between expenditure and output.
With increasing demand, only the costs of (consumable) materials and direct man-hours should rise. However, it also often appears that the indirect costs automatically increase over time, with failure costs, logistics costs and costs of direct employees also being disproportionately higher. This is largely influenced by the way in which an organizational structure is built.
Due to the functional form of organization, the process is experienced as viscous and not flexible. In order to respond more flexibly to both increases and decreases in your order book, it is therefore important to set up your organization in process flows. This is in contrast to the usual functional organizational form. Linked to a specific process, employees are better triggered to control (failure) costs and lead time without the overhead costs increasing disproportionately. Flexibility around the deployment of employees is of course crucial.
Within the lean philosophy, processes are organized as much as possible around so-called. product family groups. Thereby, as much as possible, all direct and indirect employees are linked to preferably one specific group or Flow. This means that peaks and troughs in demand will also have direct consequences for indirect employees linked to a Flow.
Organizations are constantly on the move. People often know how accurately how many direct employees are needed to keep up with the current order flow. With a (temporary) higher workload, new employees are quickly sought. But what about the indirect employees?
Often the link between order volume and required indirect hours cannot be made one-to-one, so that the ratio between indirect and direct hours can gradually grow out of proportion. Of course, one-off correction is an option. A value stream analysis, however, helps you to understand the real needs of your total occupation for both direct and indirect employees. You can also link (more) people to a specific order flow. This makes the required hours more transparent and the foundation is laid for a self-managing team. Expensive labor costs are avoided with the help of flexible employability, for example. Interested in value stream analysis and flow process design? Let us inform you what is possible!
With a high degree of standardization, lead times and costs in the form of hours and stock can be better controlled. At the same time, the period of mass production, especially for West European, companies, is no longer an option.
There is a big difference between a complete Engineering to Order (ETO) and an Assemly to order (ATO) company. Logically, your company focuses on a specific segment with associated product groups. The associated components need not deviate significantly. After all, you are not going to design your own nuts and bolts. In a Configure to order (CTO) environment, you can make handy use of already developed and thus engineered sub parts or modules. The aggregation level of these compositions naturally depends strongly on your end product and the diversity of customer wishes you want to meet. This method, developed in the automotive industry, means that your engineering must function at a higher level where CTO is central. Learn more about this topic. We have the right knowledge to help your company further!
The focus at Lean is on Flow. If companies grow strongly in turnover, it is important to create a good balance in that Flow with the help of a Value Stream Map in order to work in a targeted manner on the practical wishes of a customer and / or organization.
With a strong growth of the order portfolio in a short time, a flexible deployment of employees, for example due to overtime, is of great importance, especially if this growth was not anticipated in advance. However, if the workload remains high over a longer period, the effectiveness gradually decreases and the chance of rising failure costs increases. In addition, the turnaround time and work in progress stock will also increase rapidly. In addition to Value Stream Mapping, it is then important to start immediately with failure cost control using the Six Sigma working methods. As a rule, these provide quite a foothold for making a first optimization step. However, it remains of great importance to immediately start working with Value Stream Mapping. This way of working guarantees that proper prioritization takes place in the further streamlining of your organization. Would you like to know more about tackling failure cost control? Look at the possibilities that LMP offers!
In a functionally organized organization, capacity per department is often difficult to link to the current running order size. The balance can be restored by creating channels or product cells.
Even now we regularly see companies that have maintained a healthy order portfolio despite the crisis, but now suddenly notice a sharp drop in order intake. Intervening on the flexible work envelope often means intervening in the number of direct employees who are active in the implementation. However, it is also important to maintain a healthy balance between “office” and “shop floor”.
By organizing your activities more in flow, you also link indirect employees to a specific workflow, as it were. This makes the costs per product family group more transparent and you can therefore make better choices for the possible relocation of your employees. In order to preserve knowledge, organizations often opt for the so-called matrix model, in which the operational management lies in the flow and the functional ‘professional content’ responsibility is organized horizontally. The flexible deployment of employees makes it easier to switch and at the same time the work becomes more challenging and more varied for your employees. Such a mini cell could for instance already be formed by one engineer, one planner and one work planner who sit together and are jointly responsible for one Flow. Of course we always strive to link as many people as possible directly to a specific product family group. Want to know more about this approach? Let us know! We would be happy to visit you to discuss the possibilities.
The modular development of products often starts with the realization that simply building what the customer asks for often yields less for the customer than the concept solutions devised by the own company. It is often a question of how well you know your customer and the environment in which your product should function! After all, you are the specialist!
Your customers demand specific products that are developed and produced entirely according to their requirements. However, delivery time and price play an increasingly important role. How can you ensure that performance improves while your order continues to deliver specific work?
By standardizing your processes, errors are reduced and you are better able to optimize your own processes. Depending on the product complexity and the specific applications, it is almost always possible to elevate composite parts to standard without negatively affecting the final functionality. This not only provides great benefits for production, but also has a positive effect on (pre) calculation, engineering, purchasing, planning and logistics. Of course, the end result should fit seamlessly with the wishes of the customer. However, the question is whether a customer is always able to properly describe the functionality of the desired product. This knowledge often lies with you as a supplier! This approach naturally creates excellent opportunities for working with CTO.
Especially the hidden costs make it interesting not to have to stock every bolt size or electric motor type. After all, it is not only the bolt or nut, but also the size of the auxiliary tools and the storage space that plays a role. You can achieve great benefits by developing smart basic modules or by implementing a rationalization of your purchasing parts. In addition, it is unfortunately often also a matter of reducing an engineering culture in which a large part of the product is designed every time (specific customer requirements, preferences of the specific engineer). A more structural dialogue between Engineering and Operations is then necessary. Want to know more about this theme? Let us hear it!
Most companies work with a so-called Push model in which each step in the process is planned separately. Lean companies mainly work with Pull systems. By linking processes and working with Pull, many planning activities are unnecessary and, moreover, fewer material movements are required.
Processes are becoming increasingly complex as a company grows. For every problem or deviation that has arisen in the past, an extra step in the process is often included to ensure that such a deviation no longer occurs. This leads to wastage and is therefore a dead end.
A check on your process is sometimes unavoidable, but ultimately it adds no value to the customer. He just wants a good product. Making your process Poka-Yoke (or failure costs free) requires that your employees understand and take responsibility for the processes. Ingredients to simplify your process are: standardization (from engineering-to-order to configure-to-order), visualization of order information and workplaces, setting up product family groups and a related organizational form. In addition, if it is possible to balance capacities between the different steps within a product family group (TAKT), you may even have to cancel a large part of the planning. Of course, this does not apply to every process. However, these principles are possible more often than expected. Would you like to know more about the possibilities? We would like to share our years of experience with you.
Process optimization and automation are closely linked. Recording processes and subsequently using Accelerating automation certainly seems attractive until the Lean phenomenon is introduced. It is therefore wise to first determine your business model, which follows from the strategy, before using accelerate automation.
Many companies struggle with the question of how the theme of Lean and automation can be reconciled. How do you prevent wrong choices from being made?
Due to the introduction of Lean and therefore by adapting existing processes, it is possible that the layout of your automation system no longer meets the needs. While Lean often works with visualisations and continuous smarter organization of processes, automation is often regarded as static and therefore an obstacle. It is important to take your (future) Lean plans into account when choosing a new package. In general, it can be said that ERP (Enterprise Resource Planning) software does not hinder the introduction of Lean, but rather the way in which it was set up during the implementation. In fact, it can be an important input for building the Lean model properly. It is different with operational management at MRP 1 (Material Requirement Planning) level. Lean program components such as visualization, flow, TAKT and Kanban can, depending on the product structure, even make an important part of the management by MRP unnecessary, so that the role of, for example, a planning changes significantly. Of course, the BOM (Bill of Material) and the article structure structure will not be affected either. At the SFC (Shop Floor Control) level, the necessary matters also play a role in the registration when Lean is introduced. It is therefore of great importance, when introducing Lean, to estimate in advance at what level the Lean techniques will be deployed operationally and what consequences this will have for your automation package. More and more automation packages are now standard equipped with Lean tools. However, it remains to be careful not to purchase and equip expensive (custom) packages that may be redundant later.
In essence, Lean and QRM are hardly different. For example, both models are based on flow. Where Lean is seen more as a philosophy, QRM originated more from the POLCA model with which flow is obtained.
In practice, companies looking for new forms of management encounter many models. The question is which model suits which company best? More management models should be investigated before making a choice. What fits perfectly with the needs of a company can absolutely not function at a similar other company.
Taking personal responsibility and running the bottom up of the organization are important ingredients in running an organization in flow. Lowering inventories and achieving shorter lead times are also very important to QRM. Actually, Lean and QRM are not that different from each other, were it not that QRM is a relatively new concept that has been developed as a concept by Rajan Suri (professor at Winconson University). The main difference between Lean manufacturing and QRM is in the use of the so-called. Polca model or Paired-cell Overlapping Loops or Cards with Authorization. Unlike when working on TAKT time, POLCA “looks” a number of processing stations ahead. If capacity is available there, the order may start. This system can best be compared to a kind of ramp metering for a motorway. This prevents blockage in the flow. The model is therefore suitable for organizations with a limited number of processing stations that have many small orders with different routings. Working on TAKT according to the Lean principles, on the other hand, requires an arrangement on product family groups, but if desired, connects the entire process from order intake to delivery. TAKT time is determined on the basis of the available time vs customer demand, after which the output is calculated per unit time. In general, this allows shorter turnaround times with less inventory. However, the choice is largely determined by the routing and order size per product family group.
Agile literally means: agile, flexible.
In IT it stands for software development in short, clear periods of often no more than a month, sometimes even a week at the most. These periods are called ‘iterations’ and are, as it were, small projects. Agile is based on 12 underlying frameworks of which Scrum is the best known.
Scrum is a framework for making (software) products in a flexible way. It works with multidisciplinary teams that deliver working (software) products in short sprints, with a fixed length of 1 to 4 weeks.
The first 2 techniques were developed within the IT world where people often had to contend with endless continuous projects that often did not meet customer expectations. This was also partly caused by the fact that customer expectations often changed over time while the project was not yet completed. The Agile working methods include 12 different techniques of which the so-called Scrumming is best known. The latter “breaks down” a project into small parts, with continuous reflection between the contractor and the client. This on a weekly or monthly basis. The structure of the work has been normalized, including the associated tasks and functions.
The Lean method is a management philosophy that also uses various tools. One of the most common tools is the Kaizen combined with the Gemba. The Gemba is the location of the crime and Kaizen the framework for tackling waste in small but clear steps. In that sense, Scrum and Kaizen get pretty close together. The big difference, however, is that a Scrum process can often take many months where a Kaizen event usually lasts a maximum of 5 days. The Scrum technique is therefore now also more widely used within the technology industry for larger (improvement) projects.
Lean focuses on obtaining flow in processes. All wastes are detected and eliminated as much as possible. Six Sigma is a technique with also a set of tools that has a standardized approach to tackling complex challenges.
In addition to a set of standardized documents, statistical (mathematical) calculations are also used to determine variable process parameters. In all cases it is all about the so-called. Link Key Process Output Variables (KPOV) to the appropriate Key Process Input Variables (KPIV). A low process reliability naturally has great wastage and is therefore not Lean. However, many wastes can easily be solved with regular tools from the Lean toolbox (common sense). However, if it becomes complex, then it is time to apply Six Sigma. Six Sigma also stands for an absolute value, namely the probability of error of a process. If a process is Six Sigma, this means that there is an error rate of 3.4 defects per million possibilities (3.4 DPMO), or an error rate of 0.00034%.